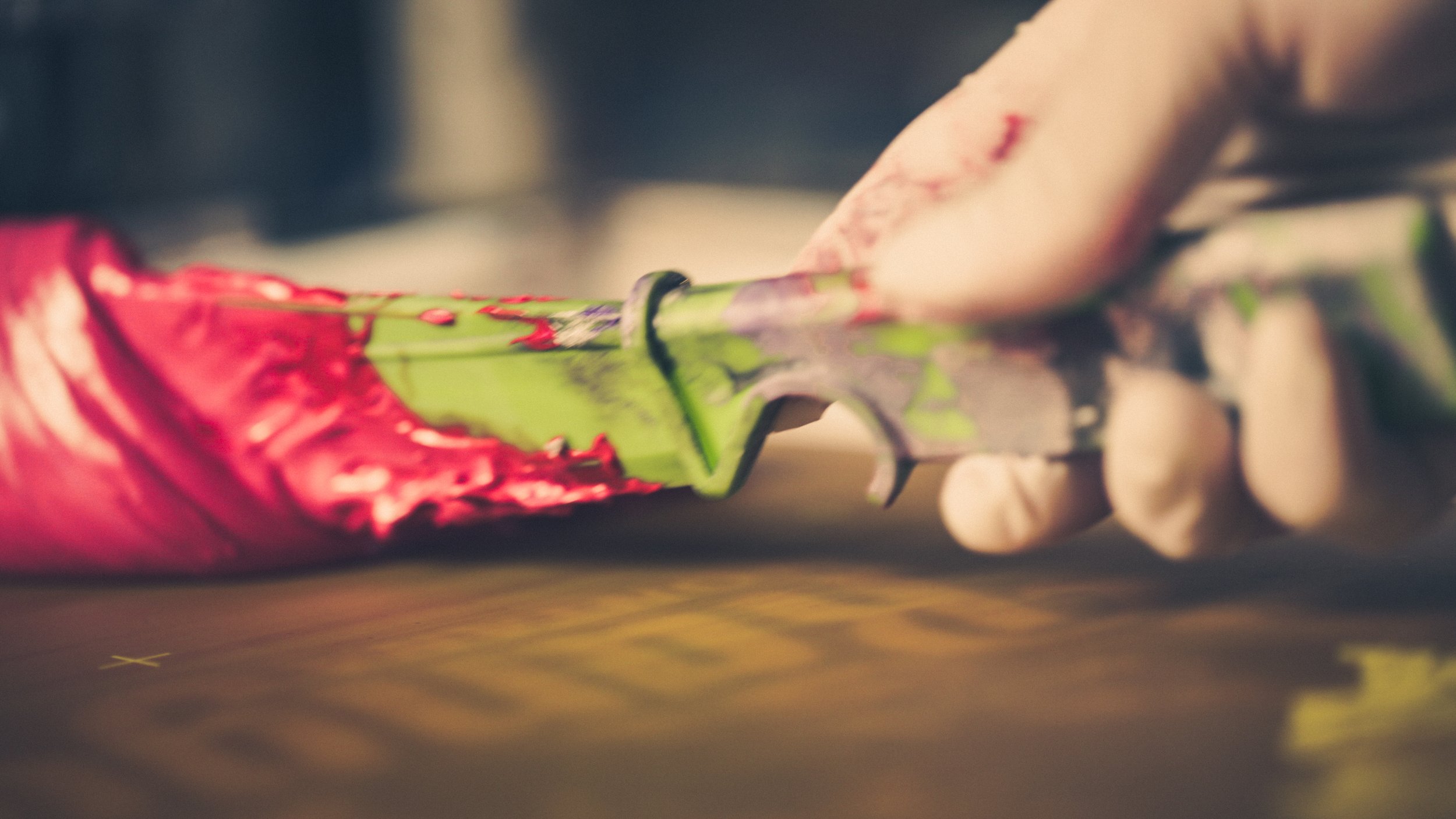
FREQUENTLY ASKED QUESTIONS
PROVIDING CLARITY TO THE SCREEN-PRINTING PROCESS
-
Screen-printing the process of converting a single piece of artwork to a combination of color-specific screens which can be set up to replicate that artwork hundreds to thousands of times and apply it to a variety of garments or paper.
Original artwork is broken down into its respective colors and each is applied to its own nylon mesh screen on which a stencil is created to only allow that color though. These screens are aligned on a manual, hand-operated printing press which allows the operator to reliably create identical prints on countless garments.
Far from being an automated process, screen-printing incorporates several technical procedures all accomplished by hand in order to develop accurate and reliable screens that can hold up to repeated use while delivering consistent results. The art of printing isn’t necessarily in the print itself, but in the entire process of setting up the job before printing can even begin.
This is why it is vital that you provide us with the highest-quality artwork from the outset to ensure a quality print on your merch.
-
Browse our list of apparel options and ink colors and submit these details along with the other information required in the online order form. Artwork can be sent via the WeTransfer link provided. If you would like to discuss alternative apparel options, please notify us in the quote request.
Upon receiving your request, we will generate a quote and digital print mockups which will be sent via our Printavo system. Once the quote is approved and full payment is received, we will begin processing your order. If you would like to change or adjust anything in your order, this discussion can happen via email and an updated quote will be provided.
You will be updated on the status of your order and given instructions for pickup or notification of shipment once your project is complete.
-
OPTIONS
Check out our Product Options page to see our recommended styles or explore the full catalogs from our wholesalers.
QUANTITIES
Our minimum order is 12 pieces per design. These 12 shirts must be identical in ink color but shirt color/style may vary.Price breaks occur at 24 pieces, 48 pieces, 72 pieces, 96 pieces, and 120 pieces.
Printing one design but switching ink colors on an order of 48 will not qualify for the price break and will be counted as two individual orders of 24
INVENTORY STOCKING
All apparel and flatstock are ordered from our wholesalers for each individual order. We do not store inventory at our shop location. Because of this, our typical turnaround time is two weeks upon approval and payment for your project. If you need your items sooner than two weeks, please reach out to us and we can discuss the possibilities for a rush order.
SAMPLES
Sometimes a digital mockup on a wholesaler website isn’t enough to get a good feel for what you will be ordering. We will gladly order samples of specific garments upon request. Samples can be examined at our shop facility during normal working hours.
APPAREL DEFECTS // PRINTING ERROR ACCEPTABILITY RATE
Although we try our best to flawlessly execute every order we print, occasionally mistakes happen. Whether due to equipment malfunction or a slight oversight on the part of the press operator, these instances are inevitable. Other times, garments may arrive with defects from the manufacturer.Considering these factors, A Thousand Arms will consider the delivery of 5% less than the quoted order quantity to be acceptable. We would encourage you to order a few extra garments per size to compensate for this potential inconvenience.
CLIENT-PROVIDED GARMENTS
If you already have apparel you would like us to print on or would like to include in a larger order, please let us know. Garments can be dropped off at our shop location during normal business hours where we will confirm the printability of your items. While we will make every attempt to execute this order flawlessly, we must consider a 5% error rate to be acceptable for client-provided apparel. -
PAPER OPTIONS
We typically use French Paper for all our flatstock printing jobs although we have the ability to order other brands if your job requires it. Standard paper weight for these jobs is 100# although French offers many heavier and lighter stocks to choose from.
INKS
We use water-based and acrylic inks on all flatstock printing jobs. These colors are matched by eye to best replicate your digital artwork. Please consider the fact that digital displays offer an unachievable level of brightness and vividness that is impossible to replicate using the screen-printing method. Slight variation of hues within these parameters will be considered acceptable. -
INK COLORS
We have a wide spectrum of specific colors we keep on hand at all times. Check out our Product Options page to see our Pantone ink library or make a request for a custom-mixed color.Ink colors have a way of shifting slightly depending on the color garment they are being printed on. We recommend printing a white under-base layer on darker color shirts to guarantee the colors of your design display accurately and vividly.
If you are looking for a specific effect such as faded/distressed or a softer feel, please include this in the Additional Comments section of the Quote Request Form and we can discuss these options further via email.
TYPES OF INK
PLASTISOL is an oil-based ink that uses heat-curing in order to bind it to the fibers of the apparel. This is our standard ink used for most apparel jobs and can be applied using a variety of techniques to achieve certain effects. Tell us what you want to achieve and we can suggest some different approaches to pull it off.WATER-BASED ink acts as more of a dye within the fabric and provides a softer-feel when fully-cured. This can be effective for specific types of looks and feels not possible with plastisol. Due to the extended curing time of this ink, prices per item will be slightly higher.
DISCHARGE ink acts as more of a bleach when applied to darker garments. It produces a softer feel similar to water-based inks. Additional logistic challenges exist with this type of ink, so further discussion will be required.
METALLIC ink contains larger particles of reflective material that make it difficult to print in high-detail, as the ink simply will not penetrate a finer-screen mesh. We would recommend only using metallic effects on areas of the print which will not suffer from a loss of detail when printed with lower-mesh screens.
PANTONE MATCHING
We can effectively match requested Pantone colors with plastisol ink only. Water-based inks provide too much variation when interacting with the pigments of the garment that it is difficult to guarantee exact results. These inks will be color-matched by eye.
INK SWITCHING
We can switch ink colors within a printing job but this will affect price breaks and overall printing charges. Please review our order minimums policy above. -
ARTWORK SPECIFICATIONS
Artwork must be supplied in print-ready condition, as outlined below. If artwork requires work on our end to get it to print-ready condition beyond the basic conversion process, hourly design rates will be charged. Our standard setup fee will be charged to adapt your design files to physical screens for printing.
ARTWORK PREPARATION
We accept most file formats, although we would prefer vector-based .ai files or layered .psd files to accommodate separation and screen preparation.Files should be at least 300 DPI resolution and sent in RGB or Grayscale color modes. When submitting halftones, please also include the layer pre-halftone in case artwork needs to be re-processed to accommodate the mesh-count of the screens we will be using for your job.
We typically use 2 pixels of trapping on overlapping and adjacent layers. White underbases are contracted by 2 pixels from the layer overprinting them.
COLORS
We will use our standard library of inks for your job and will utilize them when creating your digital mockups. If you have specific colors you would like to use, we can custom-mix Pantone colors for an additional charge. This custom color will then be added to our standard ink library. We use the Pantone Solid Coated formula guide.Colors have a tendency to shift slightly when applied to different garments when it comes to blends and colors of material. If this is a concern, please let us know and we would be happy to discuss different application methods to ensure the accuracy of your prints.
CUSTOM DESIGN
If you are in need of a design, you can check out our Design page and browse through our growing roster of talented artists. If you see something you like, get a hold of us and we can facilitate the introduction. Design time will not be factored-in to our standard two-week turnaround time.
MOCKUP APPROVAL
All jobs will be printed using our standard library of inks to replicate your approved digital mockup as accurately as possible. Please keep in mind that sizing and hues might be slightly different considering the apparel being printed on and the general process of screen-printing by hand. Slight variations within these parameters will be considered acceptable.
FLATSTOCK PRINTING
Maximum size for flatstock printing is 18” x 27.5”. We typically use 305 screen mesh with a maximum halftone threshold of 60 DPI. Please let us know if you have any concerns about the resolution of your artwork and we will be happy to advise. All artwork must have a minimum of 1/8” bleed on all sides to accommodate trimming to final print size.Several different methods can be used to reproduce your artwork to the highest accuracy possible. We can discuss further print specifics via email once artwork has been submitted.
SCREEN MESH CONSIDERATIONS
We utilize several different screen meshes depending on the job and artwork requirements. Here is a rough outline of what each is used for.110 - Typical for solid-white underbase printing and graphics with low detail. Will deposit more ink resulting in a heavier print. This mesh is the only screen used for metallic inks. Maximum halftone threshold of 25 DPI.
158 - Standard for apparel printing where more detail is required. Maximum halftone threshold of 35 DPI.
230 - Used for over-printing on apparel and is sufficient for most flatstock jobs. Maximum halftone threshold of 35 DPI for plastisol inks, 50 DPI for water-based and acrylic inks.
305 - Strictly used for flatstock printing where high levels of detail are required. Maximum halftone threshold of 60 DPI.
IMAGE/PRINT SIZES
Standard screen maximum image size is 13” wide x 15” tall.Large-format screen maximum image size is 15” wide x 20” tall.
Extra-large format screen maximum image size is 18” wide x 27.5” tall.
-
SINGLE-PASS VS DOUBLE-PASS
Depending on your artwork and the color of apparel it will be printed on, different printing methods might be required in order for it to display accurately. Darker garments typically require a double-pass of the same color or will often call for a white underbase in order to avoid dulling of the ink color requested. Double-pass and underbase printing will be noted in the printing quote.
SEAM, COLLAR AND ZIPPER PRINTING
If requested, printing over and around these areas of a garment can produce varied results. A quality print requires unobstructed contact between the screen and the garment and even slight variations can affect how evenly ink is applied to it. These requests will usually be honored, but please keep in mind that all variation resulting from these sort of applications will be deemed acceptable as finished products.
IMAGE PLACEMENT
Image location and sizing will be matched as closely as possible to the digital proofs you must approve before ordering, however slight differences may occur due to the digital mockup being merely a reference and taking into consideration the variation between smaller and larger sizes of apparel. Specific location details can be requested during the ordering process, otherwise we will use our best judgement when it comes to proper positioning and sizing if no additional specifications are added.IMAGE SIZES
When printing a run of shirts, all sizes of apparel will receive the same size print. Take this into consideration when choosing your graphics and their placement, as the same graphic will appear much larger on an XS shirt than it will on a XXL shirt. We recommend 11” as full-wide for front-chest graphics. You can certainly go larger, but there is potential for print distortion resulting from printing too close to seams or hems. Any print distortion resulting from oversize prints will be deemed acceptable as finished products.Different print sizes of the same graphic will be charged as a separate job, as it requires an additional screen to be created.
-
TAG REMOVAL / CUSTOM TAG PRINTING
If manufacturer’s tags are tear-away, we have the ability to remove these tags and replace them with custom graphics printed on the inside of the apparel in their place. We have standard A Thousand Arms graphics with the required sizing and material information that we can use. If you want custom graphics, you will need to provide them to us and be subject to our standard screen setup fees as you would for regular prints. Specifications must be followed pertaining to information regarding sizing and fabric/material content in order to be deemed acceptable to apply.
HANG-TAGS
We apply A Thousand Arms Printing hang-tags to all outgoing orders. If you would rather we not include these tags or have your own tags you would like to have us apply, please let us know in the Additional Comments section of the Quote Request Form. An additional fee will be charged for applying custom hang-tags.
FOLDING
We separate all outgoing print orders according to size and fold them in half before boxing for easy assessment and organization once you receive your order. If you have other specifications for you how would like them folded, please notify us in the Additional Comments section of the Quote Request Form. We will charge an additional fee for specific folding requirements.
BAGGING
You have the option to individually insert each shirt, folded, into a plastic bag to make them ready for retail. If you would like us to bag your garments, please notify us in the Additional Comments section of the Quote Request Form. We will charge an additional fee for bagging. -
PAYMENT TERMS
Once your quote and digital mockup have been approved, payment is due in-full before the order can be executed. We accept payment via credit/debit card or ACH. PayPal and Venmo are also accepted. Cash and check payments can also be accommodated if needed.
REFUNDS
We do not offer refunds. If for any reason you are unsatisfied with your order and your dissatisfaction results from any factor outside those addressed above, we will gladly re-print your order. -
TURNAROUND TIME
Our standard turnaround time for job completion is two weeks from the time of quote approval and payment. Garments will not be ordered from our wholesalers until both of these requirements are completed. Please note that this timetable may fluctuate based on our overall workload as well as other factors such as inclement weather or supply-chain issues. We will do our best to meet this deadline but cannot always guarantee it.
IN-HAND DATE / RUSH ORDERS
If you have a specific date you need your order in-hand, please let us know in the Additional Comments section of the Quote Request Form and we will do our best to accommodate. If this date falls within the standard two-week time window, it will be deemed a rush order and we will charge an additional fee.
SHIPPING
We ship worldwide via UPS or USPS depending on the size of your order. For domestic orders, ground shipping is our standard but expedited shipping can be used depending on the circumstances of your order.
SCREEN-STORAGE / SETUP FEES
We charge a setup fee to create your reusable screens that we will keep on hand for 1 year from time of first printing. Your first screen is included in our $50 setup fee. Each additional screen needed for your print job will incur an additional $25 fee per screen. You will not be charged a setup fee if a reorder of the same design is placed within that time period. If no reorder is placed within that time period, your screen will be recycled and you will be subjected to new setup fees upon reorder. -
SOCIAL SHARING
We will regularly document jobs being printed and upload them to our social media accounts, often inviting your band or brand to collaborate on the post, effectively sharing it to both audiences. No guarantees when this might occur but if you would like us to create this content specifically for your job, please add that request to the comments on the quote request form and we will do our best to capture the process in an appealing fashion that positively represents all entities involved.
ADDITIONAL SERVICES
A Thousand Arms provides several other services which could be of use to you after your merchandise has been printed. Product fulfillment and online store management can help facilitate effective distribution of your products if you plan on selling online. Please visit our Fulfillment page at www.athousandarms.com to learn more.
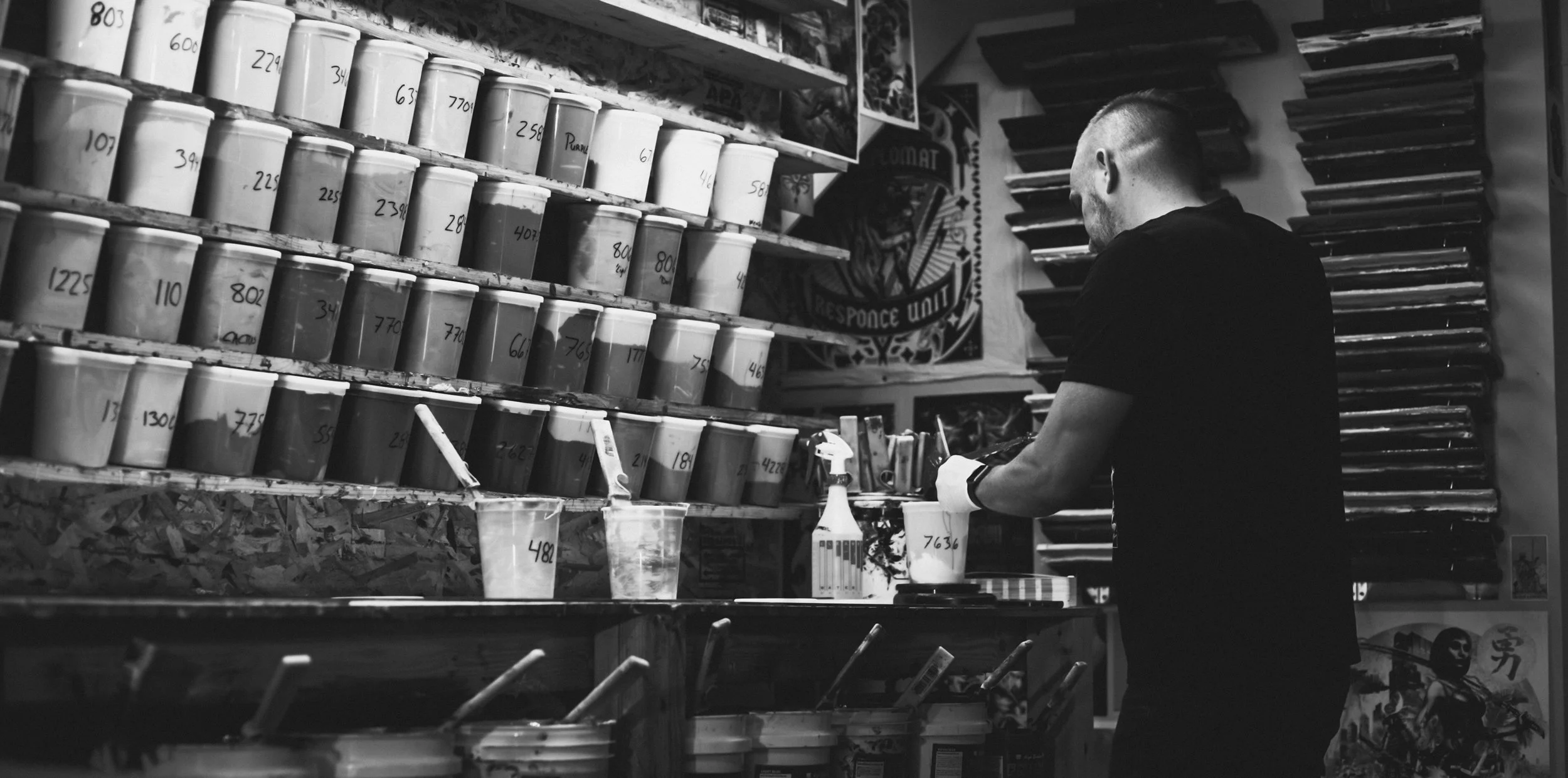
INK COLORS
MAKING IT POP
We offer a standard library of stock Pantone colors which are applicable to most print jobs.
If you require a specific Pantone color which is not in our collection, we can create a custom mix for an extra fee per color. This is recommended for branding projects where matching colors to a style-sheet is important.
PANTONE INK COLORS
OUR STOCK INK LIBRARY
Choose the colors for your design from our in-house Pantone library below. Please keep in mind that colors may slightly vary from the color you see on your screen.
NEED EXACT COLOR MATCHING?
If you require a brand-specific Pantone color, we can create a custom mix for an additional fee. We recommend this for branding projects where matching your colors is important.
Simply check the color-matching box in your quote form and we will reach out for more details.

NEED MORE HELP?
CONTACT US FOR ADDITIONAL INFORMATION
We want to make sure you’re getting exactly what you need with your screen-printing order so please don’t hesitate to reach out. We are happy to help in any way possible.

LET’S GET DOWN TO BUSINESS
TAKE THE NEXT STEP TO GET YOUR MERCH INTO PRODUCTION